Details
Drive roller is a main component of belt conveyor for transmission of power, and its mode of driving belt conveyor includes single-roller, twin-roller and multi-roller. Single-roller is mostly used on conveyors with low power, such as coal mine ground transportation and coal preparation plants. Generally, the downward belt conveyor adopts twin-roller to make it compact.
The drive roller is a main component for transmission of power, and is divided into 500. 630. 800. 1.000. 1.200 and 1.400 MM diameters according to the carrying capacity. And there are several different shaft diameters and central spans for designers to choose from for the same diameter of roller.
Light roller: bore diameter of bearing: 50–100 mm, single plate welded cylinder structure with single key connection between shaft and hub, with unidirectional shaft.
Medium roller: bore diameter of bearing: 120–180 mm: shaft and hub are connected with an expansion sleeve.
(3) Heavy roller: bore diameter of bearing: 200–350 mm, shaft and hub are connected with an expansion sleeve, and the roller body is a cast welding structure, with unidirectional shaft and bidirectional shaft.
The drive roller has exposed bright steel surface, herringbone and diamond-shaped patterned rubber cover. In case of low power, narrow belt, and dry environment, the roller with exposed bright steel surface can be used. The herringbone patterned rubber surface has a high friction coefficient, good anti-slip and drainage properties. But it is directional. The diamond shaped rubber surface is used for conveyors that move in both directions, and for rollers used in important occasions, they are covered with vulcanized rubber.
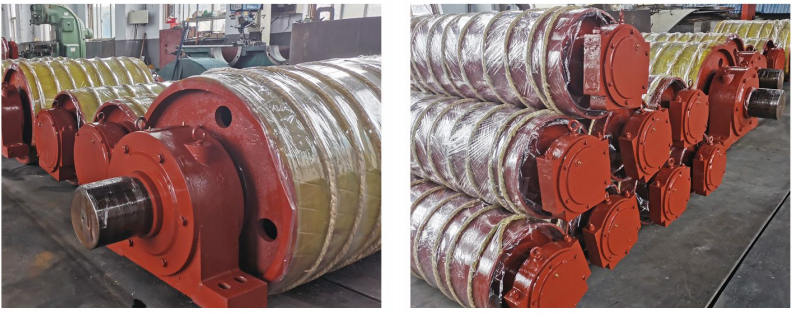
Standard Operating Procedure for Cleaning Roller
1. Dust masks and gloves must be worn.
2. The rollers must be cleaned by a designated person. Before starting, check the equipment for normal operation, defects, and loose fasteners.
3. Each batch of castings together with core iron shall not exceed 75%–80% of the roller capacity.
4.The rollers should be fixed with a pin before loading to avoid rotational injury during loading.
5.After the roller is installed with the casting, the cover should be closed and bolted. When cleaning, turn on the ventilation and dust removal equipment first, and then the roller.
6. The cover must be turned to the front side and fixed with a pin before opening the cover when removing the casting.
7. Do not allow personnel to approach when the roller is operating. Do not stack castings or other things around.
8. Do not open the cover until the impeller has completely stopped rotating when blasting and cleaning the roller.
Recommended Products